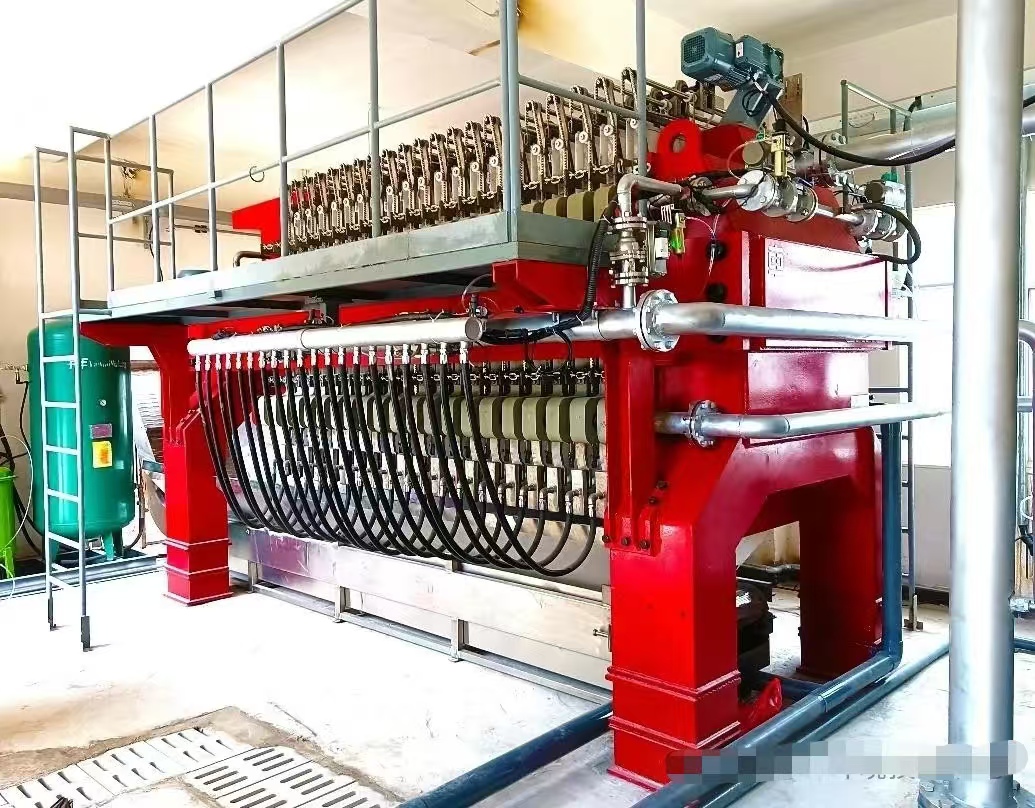
隔膜压滤机是一种理想的煤泥水处理设备, 影响压滤机运行状况的主要因素是入料压力、浓度、粒度组成和操作水平等。为了改善压滤机的工作状况,提高工作效率, 要结合选煤厂的生产实际和生产工艺, 对影响压滤机工作状况的诸因素进行合理的控制和有效的调整, 以确保压滤机高效运行。
我国选煤厂煤泥水处理系统大多选用隔膜压滤机回收煤泥, 实现洗水闭路, 但也有部分选煤厂采用煤泥离心机(高频筛) 或其他设备配合煤泥压滤机联合作业,实现煤泥回收和洗水闭路。对于前一种工艺, 压滤机入料矿浆的粒度组成基本是不可控的。但是, 后一种工艺设计则具有一定的灵活性, 即当洗煤系统(或浮选系统) 跑粗时, 可以将部分浓缩机底流合理分流进煤泥离心机, 回收粗物料, 而将离心机离心液返回压滤机入料, 这既能改善压滤机入料的粒度组成, 又可以改善压滤机工作状况。
如何提高隔膜压滤机的过滤效率呢?主要从以下几个方面来做起。
(1) 保证合理水平的入料浓度。
理论上讲, 压滤机入料浓度越高越好。浓度越高, 压滤周期越短, 可保持较大的处理量、较为理想的滤饼水分以及滤液中较低的固体含量。但是, 我国选煤厂一般是耙式浓缩机底流进入压滤机, 过高底流浓度给耙式浓缩机的正常和安全运行带来隐患, 若追求过高的底流浓度, 可能会造成耙式浓缩机压耙, 影响正常生产。所以,压滤机入料浓度应保持在400~600g/L, 这样, 既可以保证压滤机要求的入料浓度, 又可以保证耙式浓缩机的正常运转.

(2) 保持合理的入料压力。
入料压力是压滤过程的主要推动力, 入料压力越大, 压滤速度就越快, 但是, 过高的入料压力容易造成设备的磨损; 入料初期, 滤室中还没有被截留足够的物料, 严格地说滤室的封闭性还不理想, 所以, 入料阶段以及压滤初期要保持低压大流量, 压力控制在0.11~0.12MPa, 否则会造成压滤机跑料, 给后续的压滤、成饼以及卸饼带来不利的影响。压滤阶段的压力以控制在0.149~0.159MPa为宜, 但是不能大于0.18MPa, 以免压力过大对压滤机滤板、机架等造成损坏以及对入料泵无谓的磨损。现场可以通过闸阀节流调节压力, 也可以通过入料泵电机的变频调速装置实现泵扬程(提供压力) 的合理调整;

(3) 保证合理的入料粒度。
提高过滤速度:粒度合适可使物料在滤室内分布更均匀,形成的滤饼孔隙率合理,滤液能更顺畅地通过滤饼和滤布排出,加快过滤速度。若入料粒度过细,如大量小于 0.074mm 的细粒级物料,会增加物料比表面积,使颗粒间的孔隙变小,滤液流动阻力增大,过滤速度显著降低。
改善成饼效果:合理的入料粒度有助于形成结构紧密、厚度均匀、强度合适的滤饼。当入料中粗粒级物料含量过高,如大于 0.15mm 粒级物料含量较多时,可能导致滤饼松散、不成形,出现跑料现象,还会使卸料困难;而粒度过细,滤饼可能过于紧实,水分难以排出,且会增加滤布堵塞的风险,同样影响成饼和卸料。
保护设备:合适的入料粒度可减少对压滤机滤布、滤板等部件的磨损和堵塞。过粗的颗粒可能会划伤滤布,降低滤布的使用寿命,还可能在进料通道或滤室中堆积,造成局部堵塞,影响设备正常运行;过细的颗粒容易进入滤布纤维间隙,堵塞滤孔,增加过滤压力,长期可能导致滤板变形、损坏。
降低能耗:保证合理的入料粒度,能让压滤机在适宜的工况下运行,减少因粒度问题导致的过滤时间延长、压力过高或设备故障等情况,从而降低设备的运行能耗,实现节能增效。
如您在压滤机、过滤工程选型中需要更多的过滤与分离方面的咨询,欢迎来电(13732231928周经理)咨询,我们可根据您现场过滤工况和您共同做好设备方案设计和科学选型。